Spannungsrisskorrosion: Unterschied zwischen den Versionen
EWill (Diskussion | Beiträge) K |
Gbolle (Diskussion | Beiträge) K |
||
Zeile 1: | Zeile 1: | ||
− | Die Spannungsrisskorrosion ist eine Sonderform der [[Korrosion]], welche bei gleichzeitigem Vorhandensein eines Angriffsmittels und einer mechanischen Zugkraft bei empfindlichen Stählen auftreten kann. Von Spannungsrisskorrosion sind vor allem Spannbetonbauteile betroffen, welche vor 1990 hergestellt wurden. | + | [[File:spannungsrisskorrosion5.jpg|right|thumb|250px|infolge Spannungsrisskorrosion zunächst angerissener und später gebrochener Spanndraht]]Die Spannungsrisskorrosion ist eine Sonderform der [[Korrosion]], welche bei gleichzeitigem Vorhandensein eines Angriffsmittels und einer mechanischen Zugkraft bei empfindlichen Stählen auftreten kann. Von Spannungsrisskorrosion sind vor allem Spannbetonbauteile betroffen, welche vor 1990 hergestellt wurden. |
=Allgemeines= | =Allgemeines= |
Version vom 28. August 2024, 11:01 Uhr
Die Spannungsrisskorrosion ist eine Sonderform der Korrosion, welche bei gleichzeitigem Vorhandensein eines Angriffsmittels und einer mechanischen Zugkraft bei empfindlichen Stählen auftreten kann. Von Spannungsrisskorrosion sind vor allem Spannbetonbauteile betroffen, welche vor 1990 hergestellt wurden.
Allgemeines
Durch die Spannungsrisskorrosion kommt es zu keiner Beeinträchtigung der Zugfestigkeit des Stahls, allerdings nehmen die Verformungskennwerte und somit auch die Duktilität stark ab.
Die Spannungsrisskorrosion stellt eine größere Gefahr dar als andere Korrosionsformen, da sie mit geringem Masseverlust und ohne erkennbare Mengen an Korrosionsprodukten unbemerkt im Bauteilinneren voranschreiten und zu einem spröden Versagen ohne Ankündigung führen kann. Das Versagen ist auch viele Jahre nach der Errichtung nicht auszuschließen [1].
In vielen Fällen lassen sich Schäden infolge von Spannungsrisskorrosion auf eine mangelhafte Bauausführung zurückführen (z.B. Verpressfehler oder zu geringe Betondeckung), zu hohe äußere Einwirkungen oder Bauwerksschädigungen zurückführen [2]. Es sind aber auch Schadensfälle aufgetreten, in denen keine Ursache für die Spannungsrisskorrosion ermittelt werden konnte [3].
Die folgenden Voraussetzungen müssen für die Entstehung von Spannungsrisskorrosion erfüllt sein:
- Vorhandensein einer Zugspannung (z.B. durch äußere Belastungen, Eigenspannungen oder innerer Druck infolge einer Wasserstoffanreicherung)
- Anwesenheit eines Angriffsmittels (Haupteinflussfaktoren: Feuchtangebot, Temperatur, Anwesenheit von Promotoren, pH-Wert, Menge an gelöstem Wasserstoff)
- Empfindlichkeit des Stahls gegenüber Spannungsrisskorrosion (abhängig von der chemischen Zusammensetzung, dem Herstellungsprozess, der Form der Nachbehandlung und Zugfestigkeit des Stahls)
Ist eine der drei Bedingungen nicht erfüllt, findet auch keine Spannungsrisskorrosion statt. Es reicht dementsprechend eine der drei Bedingungen auszuschalten, um Spannungsrisskorrosion zu verhindern.
Das Vorhandensein von Zugspannungen lässt sich im Stahl- und Spannbetonbau nicht vermeiden, da es die Grundidee dieser Technologie ist. Auch die Anwesenheit von Angriffsmitteln kann nicht ausgeschlossen werden, da bereits eine geringe korrosive Vorschädigung, die mit bloßem Auge nicht erkennbar ist, ausreichen kann, um Spannungsrisskorrosion auszulösen. Solche korrosiven Vorschädigungen können während des Transports, der Lagerung oder des Einbaus entstehen und sind unter baupraktischen Bedingungen nicht mit absoluter Sicherheit auszuschließen. Hierbei ist vor allem die Zeit zwischen dem Vorspannen und dem Verpressen von Spanngliedern gefährlich, da in diesem Zeitraum bereits große Zugspannungen vorhanden sind in Kombination mit einer hohen Luftfeuchtigkeit und fehlendem Korrosionsschutz [4].
Da weder das Vorhandensein einer Zugkraft noch das eines Angriffsmittels ausgeschlossen werden kann, ist die einzige Möglichkeit Spannungsrisskorrosion zuverlässig zu verhindern, den Einsatz empfindlicher Spannstähle zu vermeiden. Dies wurde in den 1970iger Jahren durch die Verschärfung der Zulassungsvoraussetzungen für Stähle erreicht [5][6]. Bei Stählen, die nach 1990 verbaut wurden, kann davon ausgegangen werden, dass bei Einhaltung aller Vorschriften und unter baupraktischen Bedingungen keine Gefährdung durch Spannungsrisskorrosion besteht [1].
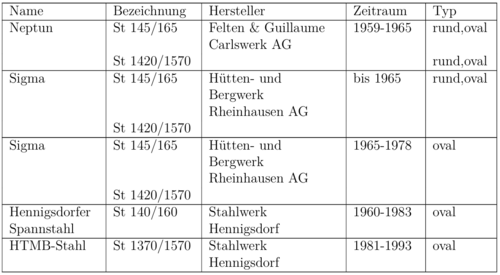
Ob Bauwerke, die vor 1990 errichtet wurden, spannungsrisskorrosionsgefährdet sind, ist abhängig davon, ob ein empfindlicher Stahl verbaut wurde. Eine Liste der als gefährdet eingestuften Stähle kann der Handlungsanweisung Spannungsrisskorrosion [7] entnommen werden. Da die Ursache für die höhere Empfindlichkeit bestimmter Spannstähle gegenüber Spannungsrisskorrosion noch nicht abschließend geklärt werden konnte [2], erfolgt die Einstufung anhand von bekannten Schadensfällen mit dem jeweiligen Stahl. Außerdem können auch Stähle, deren Zusammensetzung der von empfindlichen Stählen gleicht als gefährdet eingestuft werden.
Es sei angemerkt, dass nicht alle Chargen der als gefährdet eingestuften Stähle tatsächlich gefährdet sind. Der Anteil der tatsächlich gefährdeten Stähle an der Gesamtproduktion ist jedoch unbekannt [8]. Selbst innerhalb eines Spannglieds kann die Empfindlichkeit differieren [9].
Arten der Spannungsrisskorrosion
Anodische und Kathodische Spannungsrisskorrosion
Anodische Spannungsrisskorrosion
Bei der anodischen Spannungsrisskorrosion (teilweise auch verformungsinduzierte Spannungsrisskorrosion) ist die Korrosion in Form einer extremen örtlichen Metallauflösung der dominierende Faktor für das Versagen [10]. Sie wird durch elektrolytische Auflösungsprozesse an der Metalloberfläche initiiert [4].
Voraussetzung für die anodische Spannungsrisskorrosion ist die Anwesenheit eines spezifisch wirkenden Angriffsmittels (z. B. Nitrate, Sulfate, Chloride) in Verbindung mit einem für das Medium und diese Korrosionsart anfälligen Stahl sowie das Vorhandensein einer Zugspannung. Die Zugspannung muss dabei über der materialspezifischen Grenzzugspannung liegen [8].
Üblicherweise tritt die anodische Spannungsrisskorrosion bei Stählen auf, die an der Phasengrenzfläche zwischen Metall und Angriffsmittel mit einer Passivschicht oder einer sonstigen schützenden Deckschicht bedeckt sind. Ausgangspunkt ist eine lokale Schädigung dieser Passivschicht [9].
Die Rissbildung erfolgt interkristallin als elektrochemischer Prozess durch Herabsetzung der Grenzflächenenergie und Herauslösen der Korngrenzensubstanzen zwischen den Kristallen, infolge der Einwirkung oberflächenaktiver Agenzien wie Chloriden, Sulfaten oder Nitraten stattfinden. Außerdem ist auch eine transkristalline Rissausbreitung als physikalischer Prozess beim Auftreten von Zugspannungen über der Grenzzugspannung möglich [9].
Bei planmäßiger Verarbeitung und planmäßigem Einbau der Stähle sowie fehlerfreiem Verpressen ist die anodische Spannungsrisskorrosion im Spannbetonbau nahezu ausgeschlossen, da das Zusammentreffen aller erforderlichen Randbedingungen unwahrscheinlich ist [4]. Im Vergleich zur kathodischen Spannungsrisskorrosion spielt die anodische in der Baupraxis daher nur eine untergeordnete Rolle.
Kathodische Spannungsrisskorrosion
Bei der kathodischen Spannungsrisskorrosion (auch Wasserstoffversprödung oder wasserstoffinduzierte Spannungsrisskorrosion) ist die mechanische Belastung der dominierende Faktor für das Versagen [10]. Sie ist im Vergleich zur anodischen Spannungsrisskorrosion die häufigere Ausprägung der Spannungsrisskorrosion im Bauwesen, da für ihre Auslösung kein spezifisch wirkendes Angriffsmittel erforderlich ist [9]. Allgemein lässt sich feststellen, dass hochfeste Stähle eher zu einer kathodischen Spannungsrisskorrosion neigen [2]. Die Grenze liegt dabei ca. zwischen 1000-1200 MPa [2].
Voraussetzung für die Entstehung der wasserstoffinduzierten Spannungsrisskorrosion ist die Anwesenheit einer Zugspannung und adsorbierbarem Wasserstoff in Verbindung mit einem gegenüber Spannungsrisskorrosion empfindlichen Stahl [2]. Der Wasserstoff muss in atomarer Form vorliegen, um adsorbiert werden zu können [11]. Die Wasserstoffaufnahme allein löst noch keine Schädigung aus, erst unter der gleichzeitigen Einwirkung von mechanischen Belastungen findet eine Versprödung statt [12].
Zur Bildung von Wasserstoff kommt es im Rahmen des aus Elektroneutralitätsbedingungen erforderlichen kathodischen Teilschritts der Korrosion. In sauren bis neutralen Umgebungen bildet er sich als Korrosionswasserstoff, in stark alkalischen Umgebungen durch Wasserzersetzung [4]; teilweise ist die Aufnahme von Wasserstoff auch im Rahmen metallurgischer Prozesse bei der Stahlherstellung möglich [9]. Bereits eine geringe Korrosionsreaktion ohne gut sichtbare Korrosionsprodukte, beispielsweise infolge einer vermeintlich harmlosen Feuchtigkeitseinwirkung, kann bei stark empfindlichen Stählen ausreichen, um die kritische Wasserstoffkonzentration zu erreichen [4].
Korrosionswasserstoff Wasserzersetzung
Der im Rahmen elektrochemischer Prozesse gebildete atomare Wasserstoff wird zunächst vom Metall adsorbiert. Für die Menge an adsorbierbarem Wasserstoff ist die Geschwindigkeit der Oxidation und der Reduktion entscheidend [4]. Außerdem nimmt sie mit steigender Wasserstoffkonzentration im Medium, steigendem pH-Wert, abnehmendem Sauerstoffgehalt und zunehmender Menge an Promotoren zu [4].
Der adsorbierte atomare Wasserstoff kann im Folgenden entweder zu unschädlichem molekularem Wasserstoff, welcher die Stahloberfläche wieder verlässt, rekombinieren, unter Sauerstoffzutritt zu Wasser oxidieren oder vom Stahl absorbiert werden [9]. Wasserstoff diffundiert bevorzugt in plastifizierte Bereiche etwa an der Rissspitze, wegen der Aufweitung des Gefüges in diesen Bereichen [13]. Hierdurch kommt es an der Rissspitze zu einer erhöhten Wasserstoffkonzentration, welche in Verbindung mit erhöhten inneren Drücken im Gefüge zu einem unterkritischen Risswachstum führen kann. Unterkritisches Risswachstum meint solches ohne Überschreitung der äußeren Spannungen. Die Rissausbreitung ist daher unabhängig von den äußeren Spannungen und somit in jedem Bauteilbereich möglich [4].
Rekombination zu molekularem Wasserstoff Oxidation zu Wasser Absorption des Wasserstoffs
Bisher wurde noch kein Modell entwickelt, welches den Schädigungsablauf der wasserstoffinduzierten Spannungsrisskorrosion vollumfänglich beschreiben kann. Im Folgenden sollen die gängigsten Theorien kurz vorgestellt werden:
- Drucktheorie: Laut der Drucktheorie folgt die Rissbildung durch Spannungsrisskorrosion, aus der mit einer Volumenvergrößerung verbundenen Rekombination des absorbierten atomaren Wasserstoffs zu molekularem Wasserstoff in Gitterfehlstellen im Metallgefüge, z. B. Poren oder Mikrorissen [4]. Hierdurch steigt der innere Gasdruck im Metallgefüge, was in Verbindung mit einer mechanischen Belastung zur Entstehung von Zugkräften und einer Überschreitung der Bindungskräfte zwischen benachbarten Atomen, einer Aufsprengung des Metallgefüges und schlussendlich zur Rissbildung führt [9].
- Adsorptionstheorie: Die Adsorptionstheorie besagt, dass die Adsorption von atomarem Wasserstoff an der Rissspitze zu der Reduktion der für das Risswachstum erforderlichen Spannungen führt, wodurch ein unterkritisches Risswachstum möglich ist [9]. Die Adsorptionstheorie eignet sich nicht als alleinige Erklärung für die Wasserstoffversprödung, es findet eher eine Beschreibung der Rissausbreitung statt [9].
- Versetzungstheorie: Die Versetzungstheorie besagt, dass die Anreicherung von Wasserstoffatomen an Versetzungen, Einschlüssen und Verunreinigungen zu einer Behinderung der Versetzungsbewegungen und des Verformungsvermögens führt [9], wodurch ein Sprödbruch begünstigt wird. Diese Theorie beschreibt weniger die Rissbildung, sondern mehr den Prozess der Anreicherung des Wasserstoffs [9], kann dadurch aber eine Erklärung für verzögerte Spannstahlbrüche liefern [11].
- Dekohäsionstheorie: Die Dekohäsionstheorie ist die Theorie, welche das Prinzip der Wasserstoffversprödung für die hochfesten Spannstähle am besten beschreibt [9]. Sie beruht auf einer interstitiellen Einlagerung von atomarem Wasserstoff im Stahlgefüge, welche infolge elektrochemischer Wechselwirkungen zwischen Wasserstoff und Metallatomen zu einer Verringerung der Bindungskräfte im Metallgefüge führt [11]. Die Bindungskräfte zwischen den Atomen nehmen dabei mit steigender Wasserstoffkonzentration ab [4]. Notwendige Bedingung hierfür ist die Überschreitung einer kritischen Wasserstoffkonzentration. Diese ist werkstoffabhängig und nimmt mit zunehmender Zugspannung ab. Nach jeder Teilrissbildung muss wieder die kritische Wasserstoffkonzentration für einen weiteren Rissfortschritt überschritten werden. Ist das erforderliche Elektrolyt nur periodisch vorhanden, kann sich die Rissausbreitung über mehrere Jahre erstrecken [1]. Der eingelagerte Wasserstoff führt zu einer lokalen Zunahme der Fließspannungen, wodurch Spannungsspitzen nicht mehr durch plastische Verformungen abgebaut werden können [8]. Dies führt zu einem verformungsarmen, spröden Versagen.
Klassische und nichtklassische Spannungsrisskorrosion
Hinsichtlich der Art der Beanspruchung kann zwischen klassischer und nichtklassischer Spannungsrisskorrosion unterschieden werden. Klassische Spannungsrisskorrosion entsteht unter statischer Beanspruchung, nichtklassische unter einer Schwingung mit geringer Amplitude oder einer kritischen Dehnungsgeschwindigkeit. Die kritische Dehnungsgeschwindigkeit hat hierbei einen oberen und einen unteren Grenzwert [2]. Die klassische Spannungsrisskorrosion ist die häufigere Spannungsrisskorrosion-Form im Spannbetonbau [2].
Teilweise wurde beobachtet, dass Stähle, welche unter stetiger Belastung duktil versagten, unter einer kritischen Dehnungsgeschwindigkeit ein sprödes Versagen aufwiesen [4], d.h. Stähle, die nicht empfindlich gegenüber klassischer Spannungsrisskorrosion sind, können dennoch eine Empfindlichkeit gegenüber nichtklassischer Spannungsrisskorrosion aufweisen.
Schädigungsmechanismus
Der Schädigungsablauf der Spannungsrisskorrosion lässt sich in drei Bereiche aufteilen:
- Inkubationsphase (Rissbildung)
- Rissausbreitung
- Reißphase
In der Inkubationsphase bilden sich Anrisse, dies geschieht häufig in Korrosionsnarben, welche im Rahmen einer korrosiven Vorschädigung entstanden sind. Wenn bereits Anrisse vorhanden sind, z.B. aufgrund der Herstellung, des Transports, der Lagerung oder des Einbaus, entfällt die Inkubationsphase. Im Folgenden breiten sich die Anrisse weiter aus. Wenn die verbleibende Querschnittsfläche nicht mehr ausreicht, um die einwirkenden Kräfte aufzunehmen, kommt es zum Sprödbruch.
Die Dauer der einzelnen Phasen kann stark variieren. Der genaue zeitliche Verlauf der Spannungsrisskorrosion und die Schädigungshäufigkeit ist unbekannt [4]. Generell ist die Rissausbreitungsphase länger als die Inkubationsphase [8]. Die Dauer der Rissausbreitungsphase und somit auch die Standzeit ist dabei abhängig von dem umgebenden Medium und kann wenige Tage bis einige Jahre dauern [8].
Nach dem ordnungsgemäßen Verpressen kann wegen der alkalischen Umgebung davon ausgegangen werden, dass keine neuen Risse mehr entstehen können. Die Rissausbreitung ist aber unter Umständen dennoch möglich, da die vorhandenen Risse eventuell nicht repassiviert werden, sodass sich der pH-Wert in diesen in einem sauren bis neutralen Bereich befindet und die Wasserstoffbildung weiterhin möglich bleibt [2]. Durch dieses Phänomen können auch Schadensfälle erklärt werden, bei denen kein vorhandenes Elektrolyt identifiziert werden konnte [14]. Die Korrosionsbedingungen im Riss sind unabhängig von den Umgebungsbedingungen außerhalb des Risses und lassen sich nur schwer beeinflussen [11].
Hinsichtlich der Rissausbildung kann zwischen transkristallinen und interkristallinen Rissen unterschieden werden. Interkristalline Risse führen an den Korngrenzen entlang; sie entstehen durch eine Schwächung oder Auflösung der Bindungskräfte im Gefüge. Transkristalline Risse führen durch die Körner hindurch; sie entstehen rein mechanisch bei dominierender Einwirkung von Zugspannungen [4].
Die Bruchfläche ist in der Regel senkrecht zur Beanspruchungsrichtung ausgerichtet [4]. Im Rahmen der Spannungsrisskorrosion kommt es zu verformungsarmen, spröden Brüchen ohne wesentliche Brucheinschnürung [2]. Die Bruchfläche eines Stahls, der wegen Spannungsrisskorrosion versagt hat, kann in eine dunkle, linsenförmige Anriss- und eine mattgraue Restbruchfläche unterschieden werden [9]. Die Anrissfläche ist dabei interkristallin und breitet sich von den Anrissen ausgehend halbelliptisch aus. Wenn die verbleibende Querschnittsfläche nicht mehr ausreicht, um die Spannungen aufzunehmen, führt dies zu einem transkristallinen Restbruch [2]. In der Regel nimmt die Anrissfläche ca. 10-20% des Bruchquerschnitts ein [15]. In einem Bruchquerschnitt können mehrere Anrisse vorhanden sein [4].
Einflussfaktoren
Mechanische Belastung
Für die Schädigung infolge Spannungsrisskorrosion muss eine kritische Spannung überschritten werden. Mit steigender Wasserstoffkonzentration im Gefüge nimmt die kritische Zugspannung, welche zu einer Schädigung führt, ab [11]. Umgekehrt gilt, dass mit steigender Zugspannung die kritische Wasserstoffkonzentration abnimmt. Das Verhältnis von Zugspannung zur kritischen Wasserstoffkonzentration folgt einer Exponentialfunktion [11].
Bei entsprechend hoher Wasserstoffkonzentration können auch sehr kleine Zugspannungen Schädigungen auslösen; teilweise liegen sie sogar unter den zulässigen Spannungen im GZG. In manchen Schadensfällen reichten herstellungsbedingte Eigenspannungen oder Spannungen infolge zu kleiner Spannstahlhaspeln für die Entstehung von Spannstahlbrüchen aus [2]. Das Versagen der Bewehrung infolge von Spannungsrisskorrosion ist dementsprechend nicht auf hochbeanspruchte Bereiche begrenzt. Allgemein gilt, dass das Gefährdungspotential mit steigender Zugspannung zunimmt [9].
Auch das Verhältnis der Spannung zur Zugfestigkeit hat einen Einfluss auf die Spannungsrisskorrosionsgefährdung [9]. Dabei sind hochausgenutzte niedrigfeste Stähle weniger gefährdet als niedrigausgenutzte hochfeste Stähle. Die Standzeit von spannungsrisskorrosionsgefährdeten Stählen ist umgekehrt zur dritten Potenz der vorhandenen Spannung [16].
wobei:
… Standzeit im Korrosionsversuch … Konstante für die Werkstoffbeständigkeit im betreffenden Medium … Zugspannung aus mechanischer Belastung … Zugfestigkeit
Umgebungsbedingungen
Feuchtigkeit
Feuchtigkeit begünstigt korrosive Vorschädigungen wie z.B. Mulden- oder Lochkorrosion, welche als Ausgangspunkt für die Spannungsrisskorrosion bzw. die Entstehung von atomarem Wasserstoff dienen.
Promotoren
Unter Anwesenheit von Promotoren steigt die spannungsrisskorrosionsgefährdung, da eine korrosive Vorschädigung sowie die Wasserstoffaufnahme begünstigt wird [2]. Relevante Promotoren sind etwa Chloride und Sulfate [9], diese können durch defekte Hüllrohre, Abdichtungen oder Fahrbahnübergangskonstruktionen eindringen. Außerdem ist das Eindringen von Promotoren auch durch chlorid- oder sulfathaltige Absetzwässer während des Betoniervorgangs möglich [9]. Früher waren Promotoren teilweise auch Ausgangsstoffe des Einpressmörtels, z.B. chloridhaltige Zemente, Chloride, welche zur Verbesserung der Fließfähigkeit dienten, oder Calciumchloride, welche als Erhärtungsbeschleuniger verwendet wurden [9]. Bereits eine geringe Menge an Promotoren ist ausreichend, um die Spannungsrisskorrosionsgefährdung signifikant zu erhöhen [2].
pH-Wert
Mit steigendem pH-Wert nimmt die Spannungsrisskorrosionsgefährdung ab. Nach ordnungsgemäßem Verpressen befindet sich der Spannstahl in einer alkalischen Umgebung, wodurch die Bildung neuer Anrisse ausgeschlossen werden kann. Es besteht die Möglichkeit, dass in Rissen auch nach dem Verpressen weiterhin ein niedriger pH-Wert vorhanden ist, wodurch eine Rissausbreitung nicht auszuschließen ist.
Verpressmörtel
Von besonderer Bedeutung für die Spannungsrisskorrosionsgefährdung sind die Materialien, welche direkten Kontakt zu den Spanngliedern haben. Dies ist vor allem der Verpressmörtel. Entscheidend für die Vermeidung von Spannungsrisskorrosion ist, dass keine Fehlstellen bzw. Hohlräume im Verpressmörtel vorhanden sind, da nur durch fehlerfreies Verpressen eine alkalische Umgebung (pH-Wert=12,5-13,9 [17]) sichergestellt werden kann. Auch hier sei noch einmal darauf hingewiesen, dass die Möglichkeit besteht, dass trotz Verpressen keine Repassivierung im Riss stattfindet. Die Verwendung von promotorhaltigen Zementen ist zu vermeiden und unter Berücksichtigung der aktuellen Normung auch nicht mehr zulässig [18].
Menge adsorbierbaren Wasserstoffs
Für die Rissausbreitung bei der wasserstoffinduzierten Spannungsrisskorrosion ist eine ausreichende Konzentration an atomarem Wasserstoff erforderlich. Dieser wird in der Regel bereits vor dem Verpressen aufgenommen [11], z.B. durch eine korrosive Vorschädigung [4]. Bereits eine Vorschädigung infolge von Kondenswasser kann ausreichen, um wasserstoffinduzierten Spannungsrisskorrosion auszulösen. Auch ein Eindringen nach dem Verpressen ist möglich, wenn kein ausreichender Korrosionsschutz gegeben ist, beispielsweise durch eine ungenügende Betondeckung, eine hohe Betonporosität oder Verpressfehler [11].
Die für den Rissfortschritt erforderliche Wasserstoffmenge ist abhängig von dem verwendeten Stahl und der Höhe der Belastung. So findet die Rissbildung beispielsweise bei patentiert gezogenen Stählen bei größeren Wasserstoffmengen als bei vergüteten statt [12].
Empfindlichkeit des Spannstahls
Festigkeit
Mit steigender Festigkeit nimmt die kritische Wasserstoffkonzentration, welche zu Spannungsrisskorrosion führt, ab [2]. Aufgrund dessen sind höherfeste Stähle anfälliger für wasserstoffinduzierte Spannungsrisskorrosion als niedrigfestere. Mit zunehmender Festigkeit nimmt bei identischem Herstellungsverfahren die Spannungsrisskorrosionsgefährdung zu. Ab ca. 1200 N/mm² steigt die Spannungsrisskorrosionsgefährdung deutlich, besonders gefährdet sind Stähle mit Festigkeiten >1700 N/mm² [9].
Querschnittgeometrie
Rechteckige und ovale Spannstähle weisen eine höhere Gefährdung auf als runde. Dies liegt einerseits an der größeren Mantelfläche, über welche mehr Wasserstoff aufgenommen werden kann, und andererseits an der höheren Anrissgefahr, welche sich aus dem schlechteren Kerbfall der zumeist gerippten, rechteckigen und ovalen im Vergleich zu den glatten, runden Spannstähle ergibt [9].
Chemische Zusammensetzung der Spannstähle
In der Regel weisen empfindliche Stähle einen hohen Kohlenstoff- und einen niedrigen Chromanteil sowie ein bestimmtes Mangan-Silizium-Verhältnis auf [1], allerdings handelt es sich hierbei nicht um eine notwendige Bedingung für eine höhere Empfindlichkeit von Spannstählen [19]. Die Beobachtung abschnittsweiser unterschiedlicher Spannungsrisskorrosionsgefährdungen innerhalb eines Spannglieds widerspricht einem größeren Einfluss der chemischen Zusammensetzung auf die Spannungsrisskorrosion.
Gefüge
Sind die Korn- und Phasengrenzflächen senkrecht zur Zugbeanspruchung ausgerichtet, begünstigt dies die Rissausbreitung infolge Spannungsrisskorrosion; sind sie hingegen in Richtung der Zugbeanspruchung ausgerichtet, ist kein Risswachstum möglich [9]. Hieraus resultiert eine höhere Spannungsrisskorrosionsempfindlichkeit von vergüteten Spannstählen und eine höhere Beständigkeit von kaltgezogenen [9]. Stähle mit grobkörnigem Gefüge sind empfindlicher als feinkörnige. Hinsichtlich des Gefüges nimmt die Empfindlichkeit mit folgenden Gefügeausbildungen zu: austenitisch-perlitisch-ferritisch-bainitisch martensitisch [2]. Eine große Anzahl an Gitterfehlstellen, z. B. Versetzungen, Fremdatome, Leerstellen und Höhlräume begünstigt die Wasserstoffaufnahme und sorgt somit für eine Erhöhung der Spannungsrisskorrosionsgefährdung [11]. Mit steigenden Kohäsionskräften zwischen den Atomen nimmt die Spannungsrisskorrosionsgefährdung ab.
Oberflächenzustand
Je mehr Anrisse und Risskeime vorhanden sind, desto wahrscheinlicher ist die Entstehung von Spannungsrisskorrosion [4], da hierdurch die Wahrscheinlichkeit steigt, dass nicht alle Risse nach dem Verpressen repassiviert werden.
Herstellungsprozess
Der Herstellungsprozess beeinflusst maßgeblich die Menge und Art der Gefügeschwachstellen. Durch den Einfluss der Gefügeschwachstellen auf den Prozess der Wasserstoffaufnahme besteht ein direkter Zusammenhang zwischen Herstellungsprozess und Spannungsrisskorrosionsgefährdung. Die Anzahl an Gitterfehlstellen kann ein Indikator für die Empfindlichkeit eines Stahls sein, da mit zunehmender Anzahl die erforderliche Wasserstoffmenge für die wasserstoffinduzierte Spannungsrisskorrosion abnimmt [20]. Allgemein ist feststellbar, dass vergütete Spannstähle gefährdeter sind als warmgewalzte oder kaltgezogene [9].
Bauweise
Auch die Bauweise hat einen Einfluss auf die Spannungsrisskorrosionsgefährdung; so bieten z.B. die in der Segementbauweise erforderlichen Fugen eine zusätzliche Angriffsmöglichkeit für Korrosion. Außerdem kann bei Verwendung metallischer Hüllrohre an der Kontaktstelle von Spannstahl und Hüllrohr ein Belüftungselement entstehen [15]. Auch die Spann- und Verankerungstechnik kann die Spannungsrisskorrosionsgefährdung erhöhen.
Umgang mit von Spannungsrisskorrosion betroffenen Brücken
Bei Bauwerken, bei deren Errichtung empfindliche Spannstähle gemäß der Handlungsanweisung Spannungsrisskorrosion verwendet wurden, kann ein Versagen infolge von Spannungsrisskorrosion nicht ausgeschlossen werden. Da in der Zeit, in der ein Großteil der Brückenbauwerke in Spannbetonbauweise errichtet wurde der Einsatz der als gefährdet eingestuften Spannstähle noch zulässig bzw. deren Gefährdung nicht bekannt war, sind auch heute noch einige Spannungsrisskorrosionsgefährdeten Bauwerke in Betrieb.
Der Eigentümer, dem die Verkehrssicherungspflicht obliegt, ist dafür verantwortlich dem Nutzer ein ausreichend sicheres Bauteil zur Verfügung zu stellen.
Aus den zuvor genannten Gründen wäre theoretisch die sofortige Sperrung und Errichtung von Ersatzneubauten aller Brücken, bei denen empfindliche Spannstähle verwendet wurden erforderlich. Wegen der hohen Anzahl an betroffenen Brücken, dem hohen finanziellen und personellen Aufwand und der hohen Auslastung des Verkehrsnetzes in Verbindung mit fehlenden Ausweichstrecken ist dies jedoch nicht bei allen Brücken sofort möglich, sodass sie trotz der Spannungsrisskorrosionsgefährdung weiter genutzt werden müssen.
Eine Möglichkeit der Spannungsrisskorrosion entgegenzuwirken ist nicht bekannt [21], die Sicherstellung einer ausreichenden Sicherheit für den Nutzer muss dementsprechend auf andere Weise erfolgen. In der Regel wird eine ausreichende Sicherheit durch den Nachweis einer ausreichenden Versagensankündigung sichergestellt.
Der erste Schritt, um eine ausreichende Versagensankündigung zu realisieren ist in der Regel der Nachweis Riss-vor-Bruch gemäß der Handlungsanweisung Spannungsrisskorrosion [7]. Mit diesem Nachweis wird rechnerisch sichergestellt, dass vor dem Versagen die Rissbildung einsetzt.
Gelingt dieser Nachweis nicht, sind andere Maßnahmen erforderlich:
- Durchführung zusätzlicher Materialuntersuchungen: Mögliche Untersuchungen sind beispielsweise die Untersuchung der Spannstähle auf Anzeichen für Spannungsrisskorrosion in Form etwa von Anrissen oder korrosiven Vorschädigungen. Die Aussagefähigkeit dieser Untersuchungen ist allerdings begrenzt, da aus statischen Gründen die Spannglieder nicht auf der gesamten Länge freigelegt und untersucht werden können. Wird nur eine Stichprobe untersucht, kann Spannungsrisskorrosion auch dann nicht ausgeschlossen werden, wenn keine Anzeichen gefunden wurden, da es sich bei der Spannungsrisskorrosion um ein lokales Phänomen handelt und sich die Bedingungen für Spannungsrisskorrosion innerhalb weniger Dezimeter innerhalb eines Spannglieds ändern können. Eine weitere Möglichkeit ist die Untersuchung der Betoneigenschaften. Durch Feststellung einer geringeren Betonzugfestigkeit sind die Nachweisbedingungen günstiger.
- Einschränkung der Verkehrslast: Die Einschränkung der Verkehrslast ist, wenn möglich zu vermeiden, da die Auslastung des Verkehrsnetzes zu hoch ist und zu wenige Alternativrouten zur Verfügung stehen.
- Ersatzneubau: Ein Ersatzneubau ist aus finanziellen Gründen und wegen fehlender Planerkapazität nicht immer sofort möglich. Ein Ersatzneubau ist außerdem zu vermeiden, da er ökologische Nachteile im Vergleich zur Weiternutzung des Bestands mit sich bringt.
- Verstärkungsmaßnahmen: Bei der Durchführung von Verstärkungsmaßnahmen ist die Sinnhaftigkeit von selbigen zu hinterfragen. Durch die Verstärkung wird nämlich nur das Ankündigungsverhalten, nicht aber die Tragsicherheit bei Spanngliedschädigungen erhöht [22]. Wenn nach der Verstärkung ein auffälliger Riss auftritt, ist trotz der Verstärkung ein Ersatzneubau erforderlich, sodass die Wirtschaftlichkeit einer Verstärkung von Spannungsrisskorrosionsgefährdeten Brücken fraglich ist [8].
- Monitoring: Mithilfe eines Monitorings können Zustandsänderungen auch ohne die Entstehung von Rissen detektiert werden, sodass auch bei einem nicht erfüllten Nachweis Riss-vor-Bruch eine Versagensankündigung stattfindet. Auch wenn der Nachweis erfüllt ist, kann ein Monitoring sinnvoll sein, da bei Verwendung alternativer Versagensankündigungen Zustandsveränderungen bei einem geringeren Schädigungsgrad erkannt werden können. Mögliche Monitoringverfahren zur Bruchdetektion sind beispielsweise die Schallemissionsanalyse, die magnetische Streufeldmessung, die elektromagnetische Resonanzmessung und Durchstrahlungsverfahren. Alle zuvor genannten Verfahren weisen Einschränkungen bei der Bruchdetektion auf. Es ist noch kein Verfahren bekannt, mit dem Brüche in jeder Art von Bauteil zuverlässig erkannt werden können.
Quellen
- ↑ Hochspringen nach: 1,0 1,1 1,2 1,3 Hampel, T. et al "Untersuchung des Gefährdungspotentials älterer Spannbetonbrücken infolge Spannungsrisskorrosion in Mecklenburg Vorpommern". In: Tagungsband zum 20. Dresdener Brückenbausymposium - Planung, Bauausführung, Instandsetzung und Ertüchtigung von Brücken (2010), S. 255-267
- ↑ Hochspringen nach: 2,00 2,01 2,02 2,03 2,04 2,05 2,06 2,07 2,08 2,09 2,10 2,11 2,12 2,13 2,14 Nürnberger, U., Korrosion und Korrosionsschutz im Bauwesen, Band 1 (1995)
- ↑ Wilcke, M. et al "Betoflux - Stand der Technik in der Spannstahlbruchortung", In: Fachtagung Bauwerksdiagnose (2018)
- ↑ Hochspringen nach: 4,00 4,01 4,02 4,03 4,04 4,05 4,06 4,07 4,08 4,09 4,10 4,11 4,12 4,13 4,14 4,15 4,16 Wilhelm, T. "Wasserstoffinduzierte Spannungsrisskorrosion. Ein Beitrag zur Beurteilung der Zuverlässigkeit von Spannbetonbrücken mit Henningsdorfer Spannstahl", Dissertation, Technische Universität Dresden (2014)
- ↑ DIN EN ISO 15630-3 " Stähle für die Bewehrung und das Vorspannen von beton -Prüfverfahren - Teil 3: Spannstähle" (2008)
- ↑ DIBT - Deutsches Institut für Bautechnik "Richtlinie für Zulassungs- und Überwachungsprüfung für Spanstähle" (2004)
- ↑ Hochspringen nach: 7,0 7,1 7,2 Bundesministerium für Verkehr, Bau und Stadtentwicklung "Handlungsanweisung zur Überprüfung und Beurteilung von älteren Brückenbauwerken, die mit vergütetem spannungsrisskorrosionsgefährdetem Spannstahl erstellt wurden (Handlungsanweisung Spannungsrisskorrosion)" (2011)
- ↑ Hochspringen nach: 8,0 8,1 8,2 8,3 8,4 8,5 Lingemann, J. "Zum Ankündigungsverhalten von älteren Brückenbauwerken bei Spannstahlausfällen infolge von Spannungsrisskorrosion" Dissertation, Technische Universität München (2010)
- ↑ Hochspringen nach: 9,00 9,01 9,02 9,03 9,04 9,05 9,06 9,07 9,08 9,09 9,10 9,11 9,12 9,13 9,14 9,15 9,16 9,17 9,18 9,19 9,20 9,21 9,22 Wild, M. R. "Zur Beurteilung des Zustands von Brücken bei Spannstahlausfällen infolge von Spannungsrisskorrosion", Dissertation, Technische Universität München (2021)
- ↑ Hochspringen nach: 10,0 10,1 Böhni, H. "Risskorrosionserscheinungen bei Spannstählen", IN: Schweizerische Bauzeitung, Jahrgang 93, Heft 39 (1975), S. 603-606
- ↑ Hochspringen nach: 11,0 11,1 11,2 11,3 11,4 11,5 11,6 11,7 11,8 Moersch, J. "Zur wasserstoffinduzierten Spannungsrisskorrosion von hochfesten Spannstählen - Untersuchungen zur Dauerhaftigkeit von Spannbetonbauteilen", Heft 563, Deutscher Ausschuss für Stahlbeton (2005)
- ↑ Hochspringen nach: 12,0 12,1 Riecke, E. "Über den wasserstoffinduzierten Sprödbruch hochfester Stähle", In: Archiv für das Eisenhüttenwesen, Jahrgang 44, Heft 9 (1983)
- ↑ Isecke, B. "Neuartige Korrosionsprobleme an Bündelspanngliedern mit nachträglichem Verbund", In: Bautechnik, Jahrgang 60, Heft 1(1983)
- ↑ Engell, H. "Korrosionserscheinungen und Werkstofffragen bei Stahl- und Spannbetonbauwerken", In: Stahl und Eisen, jahrgang 98, Heft 13 (1978), S. 637-641
- ↑ Hochspringen nach: 15,0 15,1 Nürnberger, U. "Einflüsse von Werkstoff un Verarbeitung auf die Spannungsrisskorrosion von Spannstählen", In: Materials und Corrosion Jahrgang 48 (1997), S. 602-612
- ↑ Stolte, E. "Über die Spannungsrisskorrosion an Spannstählen", In: Beton- und Stahlbetonbau, Jahrgang 63, Heft 5 (1968), S. 116-118
- ↑ Holst, A. "Korrosionsmonitoring und Bruchortung vorgespannter Zugglieder in Bauwerken", Heft 573, Deutscher Ausschuss für Stahlbeton (2008)
- ↑ DIN EN 447 "Einpressmörtel für Spannglieder - Allgemeine Anforderungen" (2017)
- ↑ Bauer, T. et al. "Zur Schadensverteilung des durch Spannungsrisskorrosion geschädigten vergüteten Spannstahls bei Brückenbauwerken", In: Bautechnik, Jahrgang 88, Heft 3 (2011), S. 151-159
- ↑ Rehm, G. und Nürnberger, U. "Neue Methoden zur Beurteilung des Spannungsrisskorrosionsverhaltens von Spannstählen", In: Betonwerk + Fertigteil-Technik Heft 5 (1982), S. 287-294
- ↑ Bolle, G., Mertzsch, O. und Marx, S. "Messtechnische dauerüberwachung zur Absicherung der Restnutzungsdauer eines spannungsrisskorrosionsgefährdeten Brückenbauwerks", In: Beton- und Stahlbetonbau, Jahrgang 112, Heft 2 (2017), S. 75-84
- ↑ Albertin-Hummel, U. und Brandt, B. "Besonderheiten bei der Beurteilung des Ankündigungsverhaltens von Spannbetonbrücken nach dem Riss-vor-Bruch-Kriterium", In: Beton- und Stahlbetonbau, Jahrgang 102, Heft 9 (2007), S. 607-614
Seiteninfo
|